Budowa maszyn pneumatycznych to temat, który zyskuje na znaczeniu w różnych branżach przemysłowych. Maszyny te wykorzystują energię sprężonego powietrza do wykonywania różnorodnych zadań, co czyni je niezwykle wszechstronnymi. W podstawowej budowie maszyny pneumatycznej można wyróżnić kilka kluczowych elementów, takich jak kompresor, zbiornik powietrza, zawory oraz siłowniki pneumatyczne. Kompresor jest odpowiedzialny za sprężanie powietrza, które następnie gromadzi się w zbiorniku. Zbiornik ten pełni rolę magazynu sprężonego powietrza, które jest wykorzystywane w momencie potrzeby. Zawory kontrolują przepływ powietrza do siłowników, które przekształcają energię pneumatyczną na ruch mechaniczny. Dzięki swojej prostocie i efektywności, maszyny pneumatyczne znajdują zastosowanie w wielu dziedzinach, od produkcji po transport.
Jakie są główne komponenty w budowie maszyn pneumatycznych
W budowie maszyn pneumatycznych kluczowe są różne komponenty, które współpracują ze sobą, aby zapewnić efektywne działanie systemu. Do najważniejszych elementów należą kompresory, które są sercem całego układu. Kompresory mogą być różnego rodzaju, w tym tłokowe czy śrubowe, a ich wybór zależy od wymagań aplikacji. Kolejnym istotnym elementem jest zbiornik powietrza, który przechowuje sprężone powietrze i zapewnia jego dostępność w momencie zapotrzebowania. Zawory pneumatyczne pełnią funkcję kontrolną i regulacyjną, umożliwiając precyzyjne sterowanie przepływem powietrza do siłowników. Siłowniki pneumatyczne są odpowiedzialne za przekształcanie energii sprężonego powietrza na ruch mechaniczny, co pozwala na wykonywanie różnych operacji, takich jak podnoszenie czy przesuwanie obiektów.
Jakie zastosowania mają maszyny oparte na budowie pneumatycznej
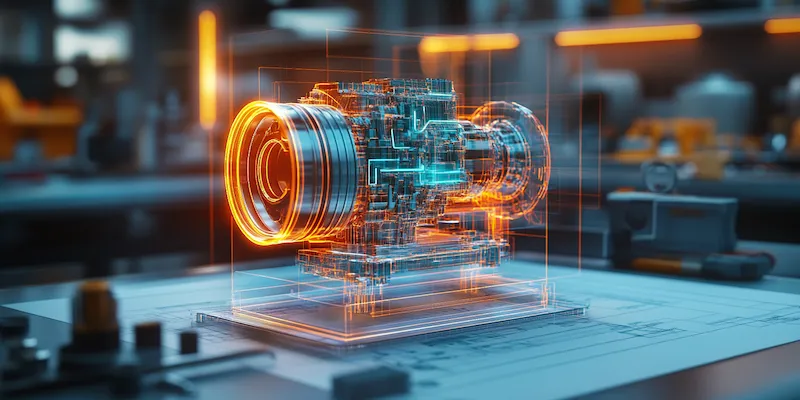
Maszyny oparte na budowie pneumatycznej znajdują szerokie zastosowanie w różnych branżach przemysłowych dzięki swojej wszechstronności i efektywności. W przemyśle produkcyjnym wykorzystuje się je do automatyzacji procesów montażowych oraz pakujących. Dzięki zastosowaniu siłowników pneumatycznych możliwe jest szybkie i precyzyjne wykonywanie operacji, co zwiększa wydajność produkcji. W branży transportowej maszyny pneumatyczne są wykorzystywane do podnoszenia i przenoszenia ciężkich ładunków, co znacznie ułatwia pracę operatorów. Ponadto w sektorze motoryzacyjnym maszyny te służą do testowania komponentów oraz jako narzędzia do obróbki materiałów. W medycynie natomiast znajdują zastosowanie w urządzeniach wspomagających rehabilitację oraz w sprzęcie chirurgicznym.
Jakie są zalety i wady maszyn pneumatycznych w budowie
Maszyny pneumatyczne charakteryzują się wieloma zaletami oraz pewnymi wadami, które warto rozważyć przed ich zastosowaniem. Do głównych zalet należy ich prostota konstrukcji oraz łatwość obsługi. Systemy pneumatyczne są zazwyczaj lżejsze niż ich elektryczne odpowiedniki, co sprawia, że są bardziej mobilne i łatwiejsze do zainstalowania w różnych miejscach pracy. Dodatkowo maszyny te oferują dużą moc przy stosunkowo niewielkich rozmiarach, co czyni je idealnym rozwiązaniem dla przestrzeni ograniczonych. Jednakże istnieją również pewne ograniczenia związane z ich użytkowaniem. Jednym z głównych problemów jest konieczność regularnego serwisowania systemu sprężonego powietrza oraz monitorowania jakości powietrza używanego w procesie. Ponadto koszty eksploatacji mogą być wyższe niż w przypadku innych technologii ze względu na potrzebę zakupu kompresora oraz dodatkowych akcesoriów jak filtry czy osuszacze.
Jakie są najczęstsze problemy w budowie maszyn pneumatycznych
W trakcie eksploatacji maszyn pneumatycznych mogą występować różne problemy, które wpływają na ich wydajność oraz niezawodność. Jednym z najczęściej spotykanych problemów jest wyciek sprężonego powietrza, który może prowadzić do obniżenia efektywności całego systemu. Wyciek ten może być spowodowany uszkodzeniami uszczelek, złą konstrukcją połączeń lub zużyciem elementów. Innym istotnym problemem jest zanieczyszczenie sprężonego powietrza, które może prowadzić do uszkodzenia siłowników oraz innych komponentów systemu. Zanieczyszczenia te mogą pochodzić z otoczenia lub z samego kompresora, dlatego ważne jest stosowanie odpowiednich filtrów i osuszaczy. Dodatkowo, niewłaściwe ustawienie ciśnienia roboczego może prowadzić do nieprawidłowego działania maszyn, co w efekcie może skutkować awariami lub przestojami w pracy.
Jakie są nowoczesne technologie w budowie maszyn pneumatycznych
W ostatnich latach w budowie maszyn pneumatycznych pojawiły się nowoczesne technologie, które znacząco poprawiają ich wydajność oraz funkcjonalność. Jednym z takich rozwiązań jest zastosowanie inteligentnych czujników, które umożliwiają monitorowanie stanu pracy maszyny w czasie rzeczywistym. Dzięki tym czujnikom można szybko wykrywać ewentualne problemy, co pozwala na szybką reakcję i minimalizację przestojów. Kolejnym innowacyjnym rozwiązaniem są systemy sterowania oparte na technologii IoT (Internet of Things), które umożliwiają zdalne zarządzanie maszynami pneumatycznymi oraz ich integrację z innymi systemami produkcyjnymi. Wprowadzenie automatyzacji do procesów związanych z obsługą maszyn pneumatycznych pozwala na zwiększenie efektywności i redukcję błędów ludzkich. Dodatkowo rozwój materiałów kompozytowych oraz lekkich stopów metali przyczynia się do zmniejszenia masy komponentów, co przekłada się na większą mobilność i elastyczność całych systemów.
Jakie są koszty związane z budową maszyn pneumatycznych
Koszty związane z budową maszyn pneumatycznych mogą być różnorodne i zależą od wielu czynników, takich jak skomplikowanie projektu, rodzaj użytych komponentów czy wymagania dotyczące wydajności. Na początku należy uwzględnić wydatki na zakup podstawowych elementów systemu, takich jak kompresor, zbiornik powietrza, zawory oraz siłowniki. Koszt tych komponentów może się znacznie różnić w zależności od producenta oraz jakości materiałów. Dodatkowo warto rozważyć koszty instalacji oraz uruchomienia systemu, które mogą obejmować zarówno prace montażowe, jak i szkolenie personelu obsługującego maszyny. Nie można zapominać o kosztach eksploatacyjnych, które obejmują energię elektryczną potrzebną do działania kompresora oraz regularne serwisowanie i konserwację systemu. Warto również uwzględnić potencjalne koszty związane z naprawami w przypadku awarii lub uszkodzeń komponentów.
Jakie są przyszłe kierunki rozwoju w budowie maszyn pneumatycznych
Przyszłość budowy maszyn pneumatycznych zapowiada się obiecująco dzięki ciągłemu rozwojowi technologii oraz rosnącemu zapotrzebowaniu na automatyzację procesów przemysłowych. W nadchodzących latach możemy spodziewać się dalszej integracji systemów pneumatycznych z nowoczesnymi technologiami informacyjnymi, co pozwoli na jeszcze lepsze zarządzanie procesami produkcyjnymi. Rozwój sztucznej inteligencji oraz uczenia maszynowego może przyczynić się do optymalizacji pracy maszyn poprzez analizę danych operacyjnych i prognozowanie awarii przed ich wystąpieniem. Ponadto rosnąca świadomość ekologiczna skłania producentów do poszukiwania bardziej efektywnych energetycznie rozwiązań w zakresie sprężania powietrza oraz minimalizacji strat energii. Możemy także oczekiwać większego nacisku na rozwój materiałów o wysokiej wytrzymałości i niskiej wadze, co wpłynie na konstrukcję maszyn pneumatycznych i ich mobilność.
Jakie są różnice między maszynami pneumatycznymi a hydraulicznymi
Maszyny pneumatyczne i hydrauliczne to dwa różne typy systemów mechanicznych wykorzystywanych w przemyśle, które mają swoje unikalne cechy oraz zastosowania. Główna różnica między nimi polega na medium roboczym: maszyny pneumatyczne wykorzystują sprężone powietrze jako źródło energii, podczas gdy maszyny hydrauliczne opierają się na cieczy hydraulicznej, najczęściej oleju. Dzięki temu maszyny pneumatyczne są zazwyczaj lżejsze i bardziej mobilne niż ich hydrauliczne odpowiedniki, co czyni je idealnymi do zastosowań wymagających dużej elastyczności ruchu. Z drugiej strony maszyny hydrauliczne oferują większą moc i precyzję przy wykonywaniu cięższych prac, co sprawia, że są preferowane w sytuacjach wymagających dużych sił roboczych. Dodatkowo układy hydrauliczne są mniej podatne na wpływ temperatury otoczenia niż układy pneumatyczne, co czyni je bardziej stabilnymi w trudnych warunkach pracy.
Jakie są kluczowe czynniki wpływające na wybór budowy maszyn pneumatycznych
Wybór odpowiedniej budowy maszyn pneumatycznych zależy od wielu kluczowych czynników, które powinny być starannie rozważone przed podjęciem decyzji inwestycyjnej. Przede wszystkim należy określić specyfikę zastosowania maszyny oraz wymagania dotyczące jej wydajności i mocy roboczej. Ważnym aspektem jest również dostępność przestrzeni roboczej – niektóre maszyny mogą wymagać więcej miejsca ze względu na swoje rozmiary lub dodatkowe komponenty takie jak zbiorniki czy kompresory. Kolejnym czynnikiem jest koszt zakupu oraz eksploatacji – warto przeanalizować zarówno jednorazowe wydatki związane z zakupem sprzętu, jak i długoterminowe koszty operacyjne związane z energią czy serwisowaniem systemu. Niezwykle istotna jest także kwestia bezpieczeństwa – wybierając maszyny pneumatyczne należy zwrócić uwagę na normy bezpieczeństwa oraz certyfikacje producenta.
Jakie są najważniejsze trendy w budowie maszyn pneumatycznych
W ostatnich latach w budowie maszyn pneumatycznych można zaobserwować kilka istotnych trendów, które wpływają na rozwój tej branży. Wzrost znaczenia automatyzacji procesów przemysłowych prowadzi do większego zainteresowania systemami pneumatycznymi, które mogą być łatwo zintegrowane z robotyką i innymi technologiami automatyzacyjnymi. Dodatkowo rosnąca potrzeba efektywności energetycznej skłania producentów do projektowania maszyn, które minimalizują zużycie energii i redukują straty sprężonego powietrza. Wprowadzenie rozwiązań opartych na sztucznej inteligencji oraz analizie danych pozwala na optymalizację procesów oraz zwiększenie wydajności pracy maszyn.